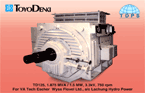
- Salient or cylindrical pole.
- Vacuum Pressure Impregnation suitable for
severe environment.
- Rated Output (kVA): 1000 ~ 50000(4 pole
rating)
- Low voltage regulation - + /- 0.25%
- Wide choice of Voltage – 415V / 3.3 / 6.6
/ 11 / 13.8 kV.
- Rated speed – 428 ~ 1800 rpm
- Frequency (Hz): 50 ~ 60. Special
frequencies on request.
- Insulation: Class F
- Bearing options – Ball / Roller / Sleeve
- Air Cooled Generators with IP 21/ IP 22 /
IP 23 Protection.
- Totally Enclosed machines with IP54
Protection
- Applicable Standards – IS, IEC,
JEC.
|
TDPS’ manufacturing facility was built in
2001 and is equipped with the latest equipment and machinery.
A strong team of around 200 staff comprising Engineers,
Technicians & staff, supports it.
TDPS has established time-tested &
proven manufacturing processes in place that require
compliance with strict quality standards right from material
selection to packing.
Design, Manufacturing & Testing of
generators are carried out under the guidance and supervision
of highly experienced Japanese specialists.
|
Pole |
4 |
6 |
8 |
10 |
12 |
Hz |
50 |
50 |
50 |
50 |
50 |
rpm
|
1500 |
1000 |
750 |
600 |
500 |
Volts |
3300/6600/11000 |
TD 84 |
800-1,200 |
600-1,000 |
600-800 |
----------- |
----------- |
TD 100 |
1,250-2,500 |
1,100-2,000 |
850-1,500 |
750-1,200 |
----------- |
TD 110 |
2,600-4,000 |
2,100-3,000 |
1,600-2,500 |
1,300-1,600 |
----------- |
TD 125 |
4,100-6,000 |
3,100-5,000 |
2,600-4,000 |
1,700-2,800 |
1,200-2,000 |
TD 145 |
6,100-10,000 |
5,100-7,500 |
4,100-6,500 |
2,900-5,000 |
2,100-4,000 |
TD 172 |
10,500-20,000 |
7,600-10,000 |
6,600-8,000 |
5,100-7,000 |
4,100-6,000 |
TD 210 |
20,250-35,000 |
10,200-18,000 |
8,100-15,000 |
7,100-12,000 |
6,100-1,000 |
TC 100 |
1,250-2,500 |
----------- |
----------- |
----------- |
----------- |
TC 110 |
2,600-4,000 |
----------- |
----------- |
----------- |
----------- |
TC 125 |
4,100-6,000 |
----------- |
----------- |
----------- |
----------- |
TC 145 |
6,100-10,000 |
----------- |
----------- |
----------- |
----------- |
TC 172 |
10,500-20,000 |
----------- |
----------- |
----------- |
----------- |
TC 210 |
20,250-35,000 |
----------- |
----------- |
----------- |
----------- |
Stators Frame is of steel
plate construction & is designed to withstand vibrations
and to ensure effective flow of cooling air.
Stator Core is made of low loss silicon
steel sheets with ventilation ducts to enable cooling of core
interior.
Stator coils are formed in diamond shape
using insulated copper strips of Class F insulation. Formed
coils are taped with required layers of resin poor tape &
the outer layer covered with Sealant tape. Over hang portion
is taped with Semi conducting tape. Individual coils are
checked for Surge before insertion. Stator coils are
inserted into the slots of core & arrested with Wedges.
Over hangs are secured with glass fiber cord to withstand
short circuit forces.
The Stator is subjected to Vacuum
Pressure Impregnation (VPI) & cured. Customized VPI
process for large generators ensures better heat transfer
capability.
Rotor Shaft is made of
Forged Steel.
Core is built out of circular Stampings
& is rigidly shrunk-fit on the Shaft.
Ventilation ducts are provided for adequate
cooling of the Rotor coils.
Rotor is provided with Damper windings on
the outer periphery of the core.
Field Winding is with polyamide insulated
Copper Strips.
Formed coils are inserted in slots &
rigidly arrested by high strength wedges. Winding overhangs
are held firmly against centrifugal forces. Larger capacity rotors are
held in the overhang by additional high strength stainless
steel rings.
For high inertia
requirements of diesel engine and high runaway speed
conditions for water turbine generators salient pole designs
are offered.
Rotor is dynamically balanced to
ensure low levels of vibration.
Depending upon the
application, output and speed, sleeve, roller or ball bearings
are provided.
Brushless exciter and
rotating rectifier assembly, mounted on the shaft of the main
Generator supplies the required excitation to the main
generator.
Permanent magnet generator as pilot exciter is
provided as an optional feature.
TDPS Generators
are supplied with digital excitation systems. One Auto &
one Manual mode is standard. Dual Auto mode (one as
hot-standby) can be provided as optional feature. Analogue
systems can also be provided on request.
At TDPS, product quality begins from enquiry /
quotation stage and extends through Design, Procurement,
Manufacturing & final inspection / testing stages.
- Utmost importance
is given to understand the performance requirements,
application and operating conditions before submitting
offers.
- Product design is
checked, vetted & reviewed to ensure compliance with
committed performance levels. Stringent quality standards
are targeted and achieved by following a systematic Quality
Plan for every Generator. The quality plan is detailed &
exhaustive and ensures adequate checks at all critical
stages right up to the dispatch of the product.
Generators are put through rigorous
testing. The TDPS set up is ISO 9001:2000 certified. TDPS
generators have been accredited by leading engineering
consulting firms.
All relevant tests, both routine and type,
are run on the finished product to ensure performance as per
IEC/IS specifications.
- Resistance measurement of all windings
- Insulation resistance measurement before
and after HV
- High voltage test on all windings
- Open circuit and short circuit
characteristics
- Phase sequence
- Voltage balance
- Vibration measurement
- Shaft voltage
- Over speed @ 120% rated speed
- Functional check of AVR with Generator
- Open circuit heat
Run
- Short circuit heat run
- Efficiency test by summation of losses
method.
- Momentary overload Test
- Sudden short circuit test @ 30% rated
voltage
- Noise level test
- Recording of no load wave form, harmonics
and THF calculation
- Determination of reactance values by
sudden short circuit test
- Vibration test
- Rotor impedance
- GD2 measurement
TDPS manufacturing facility is ISO
9001-2000 certified by TUV.
- AVANT GARDE
- M N DASTUR
- TATA CONSULTING ENGINEERS
- FICHTNER
- HOLTEC
- DESEIN
- PDIL
- DCPL
- MITCON.
- JP MUKHERJEE & ASSOCIATES and
- UHDE INDIA
- SPBPC
Technical Specification for TDPS AC Generators
|
Rated Output(kVA) 1000 to 45000
Phase 3 ,Options of 4 Leads / 6 Leads
Rated Voltage ( V ) -415,3300,6600,1100 and 13800
Frequency (Hz) - 50,60
Voltage regulation +- 0.25%
Insulation Class F
Ambient Temperature 45 Deg C
Rated Speed(rpm) -428 rpm to 1500 rpm
Construction: Cylindrical
Bearing: Ball/Roller/Sleeve Type Double/Single
Lubrication: Grease Lubricated/Oil Lubricated
Open Type IP 21/22/23 for air cooled Generators
Totally enclosed inner cooling type with air to water cooler mounted on generator IC 8A 1 W 7(side and top mounted coolers)
For totally enclosed cooling type,inlet water of 32 Deg C is used
Applicable Standards IS, IEC, JEC
|
Stator Frame: Made of welded mild steel plate construction capable of withstanding the mechanical / electrical vibrations and ensuring effective flow of cooling air.
Stator Core: Stampings are of cylindical shape, made of good quality, low loss silicon steel sfeets with ventilation ducts placed of suitable lamination thickness to enable the cooling of interior core. Finished stamping stack is rigidly welded to stator frame.
Stator Winding: High Voltage coils are formed in a diamond shape using a rectangular copper strips, preinsulated with enamel and glass covering of Class F grade insulation.
The coils are inserted into the open slots in the stator core, which are then closed with non magnetic / magnetic wedges.
The end windings are secured, lashed and braced with glass fibre cord to with stand short circuit forces. The whole stator is Vaccum Pressure Impregnated(VPI). After the impregnation and curing process, the whole unit forms a rigidly supported fully consolidated, viod free winding,
The varnish fills all the voids in the stator and results in better heat transfer from conductor to stator core.
|
Shaft - Made of forged steel
Rotor Care - Made of thin steel sheets punched in circular shape with slots. The rotor core is rigidly fitted on the shaft.
Ducts are provided in the core for proper cooling of the rotor coils. Damper windings are provided on the outer periphery of the core.
Field Winding - Flat type copper wires are bent edge wise, formed and inserted in slots, rigidly fixed by wedges.
Winding end parts are fixed by resi-glass binding enabling the construction to with stand the centrifugal force.
The wound rotor is dynamically balanced to ensure low vibration.
|
Depending upon the application, out-put and speed, the Generators are supplied with roler,ball or sleeve bearings.
Antifriction - ball / roller type are provided for small capacity generators.
Larger capacity generators are fitted with sleeve bearings.
Construction of sleeve bearings:
Two sleeve bearings with bracket type mounting.
Forced lubricating system provided as standard.
Self-lubricating system is provided for low speed generators.
Sleeve bearing with white metal on cast steel base metal.
Automatic center adjusting type supports the outer periphery by spherical seat.
Bracket provides strength to support the weight of the rotor
Labryinth consrtuction prevents the leaking of lubricating oil to outer part.
Non-drive end bearing is insulated, to prevent shaft current.
|
Brushless exciter and rotating rectifier assembly mounted on the same shaft of the main AC Generator supplies the required excitation to the main generator
|
Permanent magnet generator as Pilot exciter is provided as an optional feature for better:
Waveform since the automatic voltage regulator derives it's supply from PMG and is isolated from the AC Generator output terminal. The harmonic current from the load is prevented from passing to the AVR, thereby reducing the voltage distortion.
Positive voltage build-up, as residual is no longer required.
Ability to sustain short circuit current in the event faults.
Better motor starting capacity with lowered voltage dips.
|
All our generators comes with imported digital AVR's of BASLER & ABB make.
AVR is machine mounted in case of smaller capacity generators and a seperate AVR cum Excitation panel is provided for generators for larger capacities.
AVR cum Excitation Panel is dust-proof and vermin proteted. This panel is a free standing dust proof amd vermin protected.
This Panel is a free standing, floor mounted cubicle, conforming to IP 42 construction consisting of the following main features:
Voltage Regulation<=0.25%
Voltage Variation +-10%
One Auto and one manual mode as standard(Dual Auto mode - one main and one hot standby, can be provided as optional feature)
Soft start voltage build up
Aux QDC for paralell operation.
Volts-per-Hertz limiter.
Automatic P.F Controller.
Field flashing for shunt excitation
Excitation field ammeter and voltmeter.
DFR Unit
PT fuse protection
Field over voltage protection.
Field over current protection.
Generator under voltage protection.
Over excitation / under excitation limiter.
|
List of Elite Customers Using TDPS Alternators |
Customer
|
Rating(kW)
|
QTY No
|
Voltage Volts
|
Speed(Rpm)
|
Application
|
Country of Supply
|
Netaji Apparels
|
450
|
1
|
11000
|
750
|
Daihitsu Engine
|
India
|
Lower Menmutty a/c VA Tech
|
500
|
1
|
3300
|
500
|
VA Tech Hydro
|
India
|
Aganoor SHP a/c Boving Fouress
|
500
|
2
|
11000
|
750
|
BFL Hydro Turbine
|
India
|
Singareni Collererris a/c Powerica Ltd, Mumbai.
|
600
|
2
|
3300
|
1500
|
Cummins Engine
|
India
|
NHDC Bhopal a/c Powerica ltd., Mumbai
|
800
|
2
|
11000
|
1500
|
Cummins Engine
|
India
|
United Rice Mills
|
800
|
3
|
11000
|
1500
|
Cummins Engine
|
India
|
Toyota Techno Park
|
800
|
1
|
11000
|
750
|
Daihitsu Engine
|
India
|
Toyota Techno Park
|
800
|
1
|
425
|
750
|
Daihitsu Engine
|
India
|
Daman Machine
|
800
|
2
|
11000
|
1500
|
Cummins Engine
|
India
|
International Recreation Parks Ltd.
|
800
|
2
|
11000
|
1500
|
Cummins Engine
|
India
|
Kothari Sugars
|
800
|
1
|
6600
|
1500
|
Cummins Engine
|
India
|
KBL.
|
808
|
1
|
3300
|
1500
|
Cummins Engine
|
India
|
IIJIN Auto
|
808
|
1
|
11000
|
1500
|
Cummins Engine
|
India
|
KHI Japan.
|
1000
|
2
|
6600
|
1500
|
Gas Turbine
|
Japan
|
ISRO(International Space Research Organisation) Bangalore.
|
1000
|
1
|
11000
|
1500
|
Cummins Engine
|
India
|
Software Technology park, Cochin.
|
1000
|
2
|
11000
|
1500
|
Cummins Engine
|
India
|
Nova Iron
|
1000
|
1
|
11000
|
1500
|
Diesel Engine
|
India
|
Hind Lever Chemicals.
|
1000
|
3
|
11000
|
1500
|
Cummins Engine
|
India
|
Powerica Ltd, Mumbai
|
1000
|
1
|
3300
|
1500
|
Cummins Engine
|
India
|
* Latest Installations
|
|
|